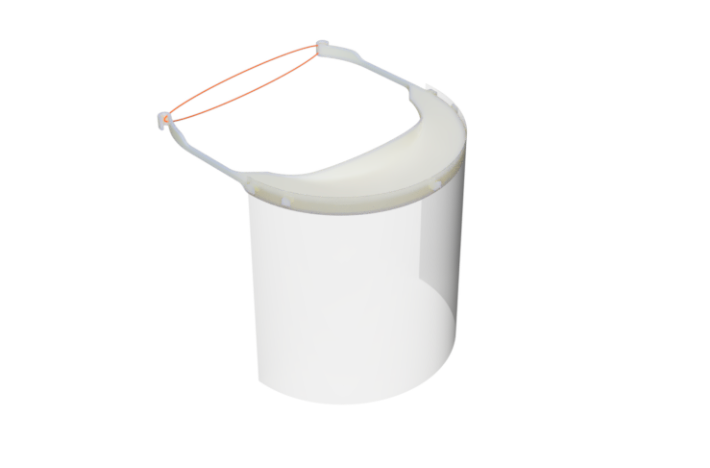
In late March, technicians of the Laney College and College of Alameda FabLabs worked together to prototype and produce face shields to help local hospitals in need of supplies as cases of COVID-19 climb in California. Dubbed the LaneyShield, their design was made of a foam headpiece, adjustable strap, and plastic shield. The first 500 LaneyShields were assembled on April 3 at Oakland’s Port Workspaces.
“We need the items, but also just the overall outpouring of support meant an incredible amount,” said Baljeet Sangha, Vice President and Chief of Logistics of the Alameda Health System. The face shields were donated to Highland Hospital in Oakland.
“Just to know that, standing shoulder-to-shoulder, there’s our community coming in to help,” Sangha reflected.
“It’s so good. It makes people feel good and made us feel good.”
Rick Rothbart, lead technician of the Laney College FabLab, reported that the production was a huge success in a video the team uploaded to YouTube. However, Rothbart said there were obstacles.
“We need to be able to make them even faster to keep up with demand here in the Bay Area,” he said. He also worried that the foam headpiece means the shields cannot be sterilized and are therefore not reusable.
Sangha shared these concerns: “Recognizing what’s happening across the country around shortages, how do we start to move towards a more reusable aspect?”
In wake of these reflections, the team chose to pivot their design. Their new vision is the LaneyVisor, which is made of a plastic shield, plastic headband, and common rubber band (such as those found in office supply stores). It’s modeled after a design created by Stratasys, a 3D production manufacturer.
“[We] made it more comfortable and more sealed off from the environment,” Rothbart said. The team plans to produce and deliver the new design to Highland Hospital in place of the LaneyShield.
“The fact that it’s solid plastic allows us to make it sterilizable and thus reusable, keeping face shields in the supply of doctors and nurses here in the Bay Area,” Rothbart said. Unlike the original LaneyShield, the visor is injection molded, meaning that the headpiece is produced by pouring thermoplastic into a mold.
“The advantages here are that injection-molded parts are super fast to make, and they’re super cheap,” Rothbart said.
The team has partnered with Wright Engineered Plastics, a Santa Rosa company that offered to produce and donate the injection mold needed for the headpiece of the visor. It will take about three weeks to complete. Rothbart said that once the injection mold is ready, the team is expecting to produce 18,000 LaneyVisors per week.
“Recognizing what’s happening across the country around shortages, how do we start to move towards a more reusable aspect?”
-Baljeet Sangha, Vice President and Chief of Logistics of the Alameda Health System
The new visors, Rothbart reported, cost about two dollars and fifty cents to produce. (The cost of producing the previous LaneyShield design was about five dollars each.) To pay for the shield materials, the team is asking for donations via a GoFundMe account. The LaneyVisors will be donated to Highland Hospital and others that request supplies. All the money will go directly to Wright Engineered Plastics, which is where the LaneyVisors are being produced.
In addition to producing the masks, Rothbart said that the designs for both the LaneyShield and the LaneyVisor are posted online for free public access.
Peralta Advanced Design and Manufacturing (ADAM) students have become involved with PPE efforts as well, by sewing surgical masks from home. One such student, Elaine Wu, spoke of College of Alameda’s link to the vast network of efforts happening around the Bay Area. Wu said that Bay Area volunteers, including those working through the FabLab, are largely rooted with a Facebook group called Make Me PPE Bay Area.
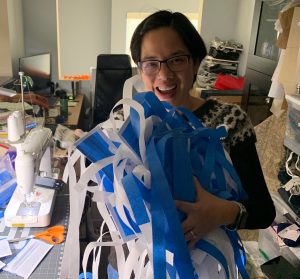
The process of producing and distributing masks is long and collaborative. Wu said that materials are pre-cut with laser cutters and put into kits by the College of Alameda FabLab. The kits include straps, face mask material, and nose wires. In the future, Wu said, the FabLab will also distribute 3D printed pleating jigs, which aid sewing the masks.
The kits are distributed to ADAM students available and able to volunteer from home. Once completed, masks are returned to the FabLab at College of Alameda, and then delivered to Make Me PPE Bay Area coordinators. The masks are sanitized and then distributed to local hospitals, nursing homes, police officers, or other essential workers.
Wu said that being involved in such a movement has been humbling and eye-opening.
“Here I am, just a student sewing masks, but I am like a speck of dust compared to everything else that is going on,” she said.
“And it is just like, wow, such a show of humanity.”
Wu said that so far, she’s sewn about 150 masks. Each one takes 15 to 20 minutes to make.
“I just have to say: I love my teachers. The quality of education that I’m getting is amazing,” Wu said.
“I could not be sewing what I’m sewing without that education.”
Their generosity will not go unnoticed, Sangha said.
“We’ll look back and realize that the Laney College team leaned in and stepped in with us in a way that we are very, very lucky and very humbled to have seen.”